
900 m², the creation of a 3D printer is shown from the design to the production and assembly of the mechanical part to the shipping to the end customer.
LEARNING FACTORY ROOM 122 SERIAL
The T U Wien Pilot Factory Industry 4.0, as learning, innovation and demonstration factory for smart production and cyber-physical production systems, focuses on new concepts and solutions for a multi-variant serial production in the field of discrete manufacturing industry, which are typical for many Austrian companies. OLYMPUS DIGITAL CAMERA TU Wien Pilot Factory Industry 4.0 By combining the refurbishment strategy with these technological topics, this learning factory is a demonstrator of how the Industry 4.0 revolution can have sustainability at the centre. This technology allows for the hands-on exploration of these and other topics, on-site or remotely. An IEC 61499 runtime environment capable of running Python function blocks was integrated with the learning factory.
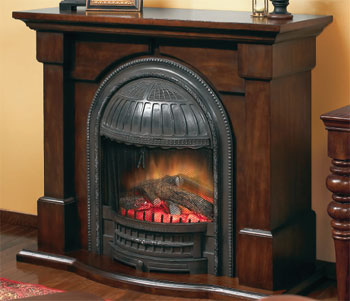
These nuggets explore the topics of Zero Defects, Condition Monitoring and System Integration. While the repurposing itself is an important lesson, a set of three additional learning nuggets was created. In FEUP, the concepts of industrial refurbishment and retrofitting are explored in the implementation of a learning factory. This modernization can sometimes be misleading in the way it is implemented, leading to the disposal of old but functional assets. The transition to the fourth industrial revolution brings with it a modernization of the shop floor. Sustainability alongside efficiency constitutes a top priority for the industry nowadays. FEUP Learning Factory for Intelligent Manufacturing This includes machinery retrofits, installation of sensors for quality inspection and process monitoring purposes, use of digital twin techniques for process performance optimization and machine diagnostics, integration of condition monitoring and predictive maintenance methods, as well as data processing and evaluation in cloud. The STUBA LF is focused on shop-floor digitalization and undergoes adaptation of its technical infrastructure towards the I4.0 concept. Thanks to the versatility of production elements and the control system, the same resources can be used and optimized to perform different operations. The testbed enables experimentation with available devices or the connecting of new devices.
LEARNING FACTORY ROOM 122 SOFTWARE
Universal robotic and production cells, including collaborative robots and machine tools, are intra-logistically interconnected by a fleet of mobile robots and vehicles by software and data also at the level of the so-called edge equipment and through server and cloud applications using artificial intelligence algorithms. The latest technologies are designed for research and development of applications for industrial practice.
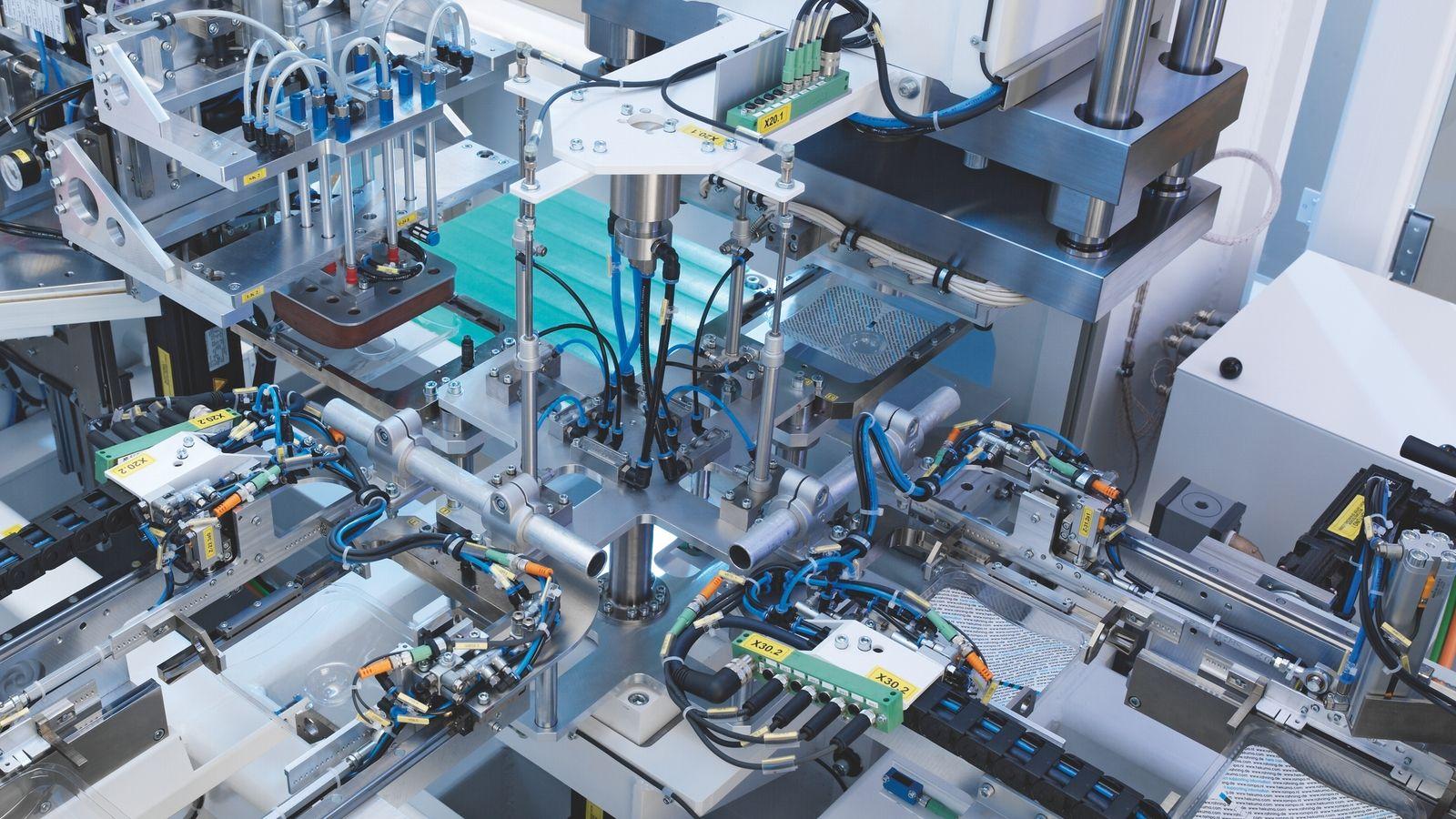
The lower floor of the testbed in the basement is focused on production technologies and production machines, while one floor above there are modules designed for flexible production. The two specifically focused floors of the testbed together create a completely unique environment for testing, simulation and development of various scenarios for smart factories of the 21st century. The Testbed is a unique research facility for the development and testing of innovative solutions for advanced and fully integrated industrial production and processes for smart factories.
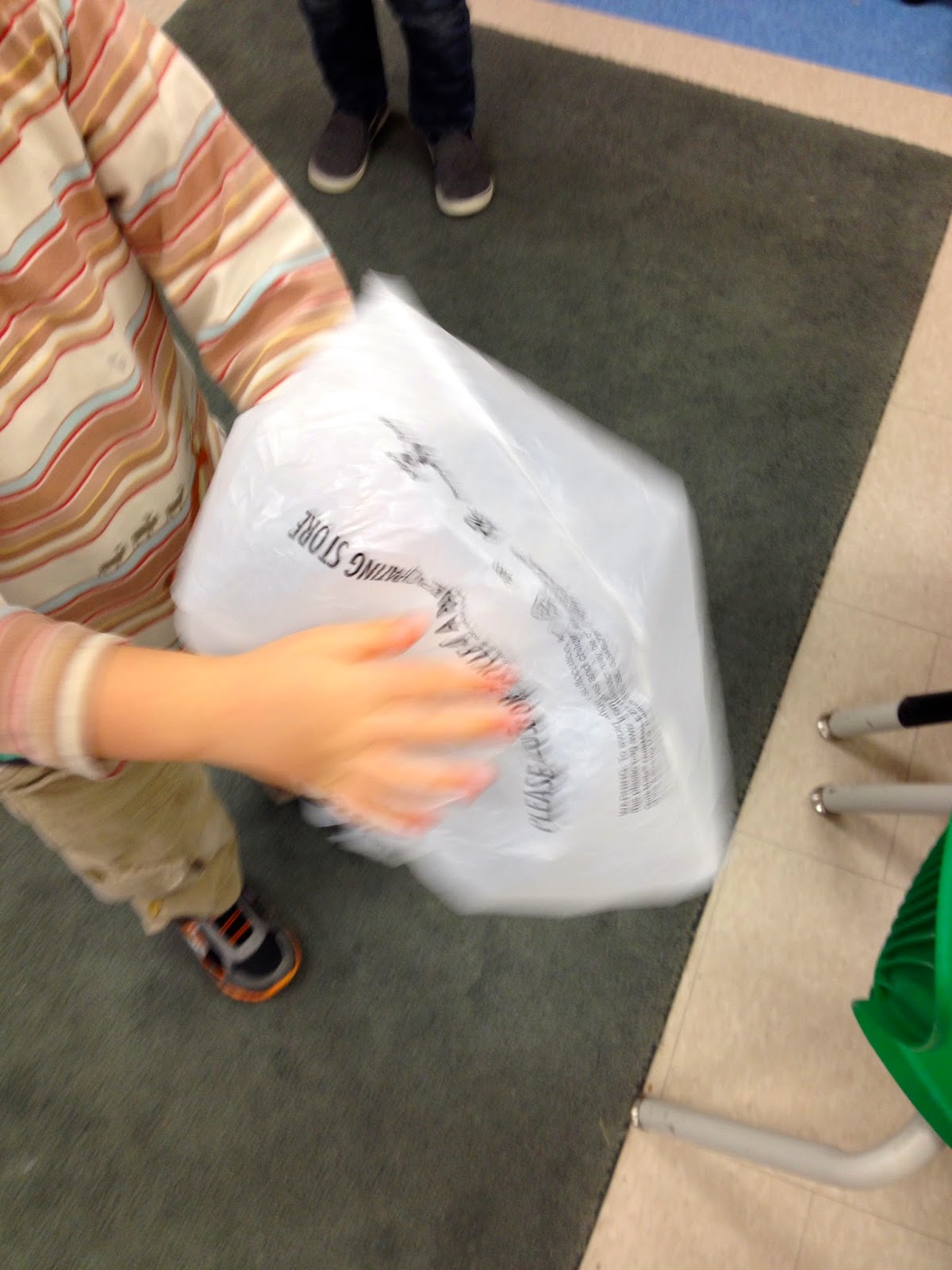
The Testbed for Industry 4.0 at CIIRC CTU as an integral part of RICAIP and as a research and experimental workplace is the core asset for the exploitation of results of multiple research projects. What other statistics do you think are relevant to the PM industry is it continues to evolve? Add them in the comments below!ĭon’t want to become a statistic? Capterra offers a directory of over 500 different kinds of project management software products to help project managers find their software solutions.CTU Testbed for Industry 4.0 at CIIRC CTU (Source: PM Solutions) < (Source: InformationWeek <